近年来,我国以前所未有的力度和决心推动氢能和燃料电池产业的创新发展,一系列重大战略和政策措施相继发布,国家相关部委和地方政府也密集出台了多项产业政策和规划,引导和推动氢能及燃料电池产业的发展。但在全球范围内燃料电池汽车的发展依然很缓慢,需要解决的技术、成本、安全等问题多多,不可一蹴而就,无论是政府还是产业界都需要理智看待燃料电池汽车的发展问题。目前,我国已经进入氢能和燃料电池产业化的初期,成本问题是制约产业发展的主要因素。
氢能是一种二次能源,不可以直接获得,需要通过制备获得,目前制氢技术主要有传统能源和生物质的热化学重整、水的电解和水的光解。对比几种主要制氢技术的成本,煤气化制氢的成本最低,规模化制氢成本约为11元/千克。其次是天然气制氢约为14元/千克,甲醇裂解约为20元/千克。成本最高的是水电解,约为40元/千克。煤气化和天然气制氢虽然价格较低,但不可持续,不能解决能源和环境的根本矛盾。而电解水制氢是可持续和低污染的,是未来主要制氢方式。随着电价下降和技术发展、规模化效应,成本会随之下降。据业内专家预测,到2020年,制氢成本可降低至20元/千克左右,到2030年实现9元/千克以下。
另外在储运方面,考虑到氢气运输在安全方面的特殊性,氢气储存和运输成本居高不下,每立方米约为9元,远超过制氢成本。但从技术层面,大幅降低氢气储存和运输成本还是有望可期的。现阶段,我国仍普遍采用35兆帕压力标准储运氢气,而日本、美国已达到70兆帕压力标准。要提升储运能力,“下一步还需从技术层面入手,运量上去了,折算下来的成本也就相应下降。”有专家表示。
从产品来看,氢燃料电池汽车的成本要远高于纯电动汽车。目前国内一辆氢燃料客车的价格在300万元以上,燃料电池成本约占整车成本的60%。而燃料电池的核心系统是电堆,其成本能占到整个燃料电池的60%左右。从电堆的成本构成来看,尤以铂系催化剂和质子交换膜为主。根据目前的市场现状,一平方厘米的nafion膜(杜邦公司质子交换膜型号)需要几元甚至近十元人民币,而每一辆车用燃料电池对质子交换膜的需求都是平方米级别的,这就意味着一个燃料电池电堆中,包含有几万甚至十几万的成本完全是归于质子交换膜的。燃料电池堆(主要包括双极板、质子交换膜、催化剂)目前基本依赖进口。特别是质子交换膜燃料电池的关键核心材料技术上落后于美国、德国和日本,最优质的质子交换膜被美国杜邦公司长期垄断。因此,依靠国产化技术探索,开发新型制备工艺是目前降低质子交换膜成本的必由之路。
从现有的技术与市场出发,专家认为,未来燃料电池成本的降低可以从三个方面入手:
一是优化材料和创新制造工艺;
二是利用规模化效应降低量产成本;
三是建立标准化平台化的体系。
原材料价格昂贵或工艺不完善的部件,例如催化剂、质子交换膜、双极板等可以通过优化制造材料改进制备工艺的方式降低成本,现有技术已经较完善的部件可通过建立标准化平台化的产品体系并利用规模化生产的效应有效建立成本优势。
除了以上燃料电池发动机关键部件的成本外,其他的材料成本会随着规模化的发展,大幅下降。据了解,国内研究机构已推出新一代质子交换膜,其拥有更低的成本及更高的质子传导率,传导率达到美国杜邦公司型号Nafion117质子交换膜的1.78倍。在成本方面,相比目前市场主流产品价格能降低10倍左右。
加氢站是氢燃料电池汽车产业链中的重要一环,因为投资巨大,在一定程度上制约了这个产业的规模化开展。据中国工业报记者了解,目前我国运营的加氢站有16座,其中固定站8座,撬装站8座,在建的加氢站有36座,距离2020年目标建成100座还相差较大,与欧美日等发达国家和地区已经约有300座商业化运营的加氢站相差较远。业内人士将加氢站与氢燃料汽车的关系比作“鸡和蛋”的关系:没有足够的加氢站,氢燃料汽车的推广应用必然受限;没有一定数量的汽车推广,加氢站也难有市场。
目前加氢站建设投资较大。中国科学院大连化学物理研究所研究员、全国燃料电池与液流电池标准委员会主任委员衣宝廉曾表示,不算土地,一座日加能力在200公斤的加氢站的建设成本至少在1500万元左右,远高于加油站和充电站,这对不少企业形成了较高门槛。加氢站的建设需要国家整体规划布局和在政策上的大力支持。

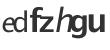
- 最新评论
- 我的评论