图为深圳赢合科技股份有限公司副总裁于建忠先生发表主题演讲
为了帮助企业客观分析2016年动力电池行业运行情况,正确把握行业发展趋势,加大动力及储能电池的开发应用,由中国化学与物理电源行业协会和电池中国网联合主办,双登集团股份有限公司、共同承办的“2016年第五届中国电池市场年会暨2016年第一届动力电池应用国际峰会、2016年第二届中国电池行业智能制造研讨会”于11月14日在北京拉开帷幕。本次年会聚集了来自政府主管部门领导、知名科研机构专家、新能源汽车动力电池产业链上中下游的企业家、投资机构代表以及媒体记者等500(这里根据现场具体人数再做调整)多人参会。
在本次会议上,深圳赢合科技股份有限公司副总裁于建忠先生做了题为《锂电智能产线发展趋势探讨》的专题报告,以下是根据速记整理的内容,未经本人审核,仅供参考。
于建忠:各位嘉宾、各位领导,大家上午好!非常感谢协会给予这样一个机会来给大家进行报告。因我是赢合科技的于建忠,我今天的议题是关于“锂电智能产线发展趋势探讨”,可能大家在动力电池行业里面,昨天一天的讨论可以看到,新能源汽车里面我们现在最大的一个核心之一就是电池,在电池工艺跟复杂程度可能我们这里很多客户也做过客户,我就从我们设备的高度出发,来探讨一下我们电池智能制造怎么来做,它的趋势是什么,我们自动化装备的标准是什么,一直在谈我们设备要实现自动化,我们工厂要实现自动化,标准是什么,要实行智能制造,我们智能制造的标准又是什么。所以在探讨这个之前我想用这个机会来给公司打个广告。
我的报告里边大概分了四个部分,因为我们整个赢合科技在去年走入资本市场,所以说可能有部分人对我们公司还不是太熟悉,所以我在这里给大家简单的介绍一下我们公司。
这是我们公司的一个宣传片,大家看一下。
这个是我们公司的一个宣传片,我用几个数字讲一下公司的历程。第一,我们公司成立10周年,现在我们定位就是动力智能生产线的解决方案,从我们这么多年,从去年进入资本市场以后,我们整线运营的经验,就是整线的解决方案得到的一定的成绩,当然我们也碰到了一些问题。包括我们最开始的时候也受到了一些质疑,我们在做这种整线解决方案的时候到底有没有能力来做这个,从现在的实践证明来看,我们会坚定不移的沿着这个线走下去。现在为止我们研发能力已经超过了450人,整个雇员公司里面超过2200人,固定资产12.3亿来适应我们整个锂电工艺的发展,我们下面有多家子公司在做不同的工艺路线的设备。这是我们今年上半年的一些举措,包括我们的架构调整,包括我们在日本设立研究院,为了提升我们整个制造装备的水平。
如图,这是我们公司的分布,包括日本研究院,和子公司的情况,现在我们生产基地是在广东省惠州。这是我们一个科研中心,这是我们大型的装备中心,这是我们的产品目录,我们现在整个产品已经涵盖了动力电池生产工艺铝壳的、软包的包括镍氢的动力生产线,我们是在今年9月份的时候第一条镍氢全自动的生产线下线,现在正在调试投入运行阶段。我们的整线解决方案是从客户开始,提供厂房图纸、基本工艺、一些基本的要求,通过深入的探讨以后做这种整套动力生产线的一个解决方案。
再来看一下关于动力电池行业的趋势分析。对于整个动力电池行业,根据相关媒体的统计,我们在2020年全球锂离子电池市场的规模将超过2亿KWh,实际上昨天的报告看,我们新能源汽车到2020年,从200万辆—500万辆不等,这个市场可能我们还受制于装备水平电芯材料或者技术的发展,会对我们造成一些困扰,我想通过材料、装备包括电池工厂大家一起的努力,我想技术上面的突破应该是会满足我们现在整个新能源汽车行业的需求,增量上面我比较看好。
按照我们政府的规划,到2020年的时候,200万辆—500万辆,如果按照新能源汽车动力电池平均带电量80KWh来算,500万辆就达到400亿Wh,从这个电池需求量来看,我们整个设备的利好市场应该是会有5年左右,这是我对整个设备产业上的一个估计。
根据我们平安研报的销售预算,锂电的生产中心大家也看到,进一步向中国在转移,我们的规模顺应了我们锂电的生产包括锂电厂的设立。第三,我们国产设备品质是有进一步提升的,大部分设备上基本上我们已经替代了国外,或者正在向国外的设备看齐。我们国内的设备,其实本身原来的起点是比较低的,我们从模仿、从学习到逐渐的接近,到后续进一步的超越,这个上面,为什么我能在这里讲这个话?是因为我们整个中国市场的土壤,可以给我们足够多的时间跟经验来摸索,这是我们整个设备行业里面想得到快速发展的一个基础。自动化设备智能化跟自动化是一个趋势,锂电设备对自动化的柔性化、自动化的精度要求也越来越高,我们到2020年整个设备的产值估计高达285亿。
关于整个设备行业我们讲的SWOT来分析,首先我们现在的优势,刚才我也讲了,下游市场的需求导致我们这两年整个设备锂电行业是爆发式增长,预计我们今年的合同金额就会高达将近15亿,这是我们整个赢合科技的,可能还有很多同行也取得了不错的成绩。第二,我们国内的技术进步比较快,不管是动力电池大的铝壳还是大的软包工艺上的革新,或者是我们在一些工艺的验证上面,我们的开发周期相对也是比较短的。第三,国内设备的价格相对国外设备是比较便宜的,在整个性价比上面,稍候我也会对整个设备行业我们的价格来源,应该是做到什么样的程度,来满足我们整个市场的需求。第四,我们国内设备的适应我们国内的开发周期跟工艺变更的变化,这个配合上面,我们相对国外设备一个非常大的优势。第五,政府的扶持跟产学研的结合。
我们的劣势是什么呢,我们的设备精度其实是不高的,整个从日韩的设备也好,从跟欧美的设备来比较也好,我们在加工精度、装备精度上面确实存在一些差距的。我们跟日韩、跟欧美设备比较的时候,我们的优势很明显,就是我们在整个实验线跟产品线,产品非常丰富,欧美或者日韩他们整个电池土壤,其实欧美基本上不生产定尺的,像刚才讲的A123、金霸王这些,整个国内市场里面,因为我们的非标自动化的开始,包括可能各家的工艺、电池大小都不一样,在这个上面我们的实验土壤是相比国外的设备优势非常明显。第四,我们其实整个设备行业里面快速发展,要求我们整个设备制造周期非常短,这里也导致我们在这上面处于比较多的劣势。第五,设备的一些通用性上。
我们现在整个市场现在是一片火爆,设备的自动化要求也是电池行业要求越来越高。来自于设备行业的一些威胁,首先是电池企业跟我们的设备厂沟通上是存在一些问题的,大家在制定方案的时候,在细节上投入时间是不够的,企业的制造水平参差不齐,我们也是一步一步走过来的,在上面有深刻的体会,包括一些价格战,是我们现在碰到的一些威胁。包括各个动力电池厂大家的工艺,可能在一些想法上也是各有各的想法,所以的工艺不确定性也导致我们风险的存在。
到现在为止我们做了将近10几条整线的动力电池生产线来看,我大概把整个电池工艺做的一个简单的矩阵。现在的工艺里边,包括叠片卷绕、软包跟铝壳,现在有1314组合的有2324组合的,其中还有比较特别的工艺,比如率料壳,甚至叠片加卷绕再放到铝壳里面,整个矩阵来看,现在动力电池的工艺无外乎就是这个简单的组合。我们在整线设备上投入,从现在情况来看,打个比方,我们的铝壳电池以年产2亿安时为准,设备商的投入大概在1元人民币左右,就是1安时,折旧大概在2毛钱,在固定资产投入上,当然跟我们电芯单体的大小,或者我们电芯批量生产的大小是有关系的,就是你的产量是有一定关系的,这个是简单的一个预估,从这几年的设备成本来看。
关于打造智能产线的探讨,我们怎么来做智能产线。现在电池制造行业里面我们面临的一些挑战,其实这个是因为我们在做智能制造上面碰到了一些问题,就是订单何时交付、何时生产,这个是我们电池行业里面,原来我们做3C类产品碰到的最大的问题就是量多样少,可能每一个产品要求的尺寸、规格都不一样,品种非常多,但是它的量是很少的。现在我们动力电池其实走的路线是样少量多,我可能固定的1—2个型号,可以打批量的生产。整个制造周期上生产安排会不一样,怎么减少浪费,如何保证产品质量,如何制造有效的召回政策,因为整个汽车市场安全性对我们来讲挑战很大。我们在实现单机智能化以后,我们的产线连接、多工厂之间的连接,我们的需求变更、生产技术的变更,包括我们的忧虑,包括我们的能源差异性等等如何保证,因为我们整个电池工艺制造周期比较长,从我们现在接触的电池客户来看,9到20几天的都有,我讲的是一个电池从投料到产出的情况。所以在这个行业里面我们其实面临了很多挑战,包括我们整个电池在制作过程中它的形态是变化的,它开始是可见的,后续我们的浆料、磨卷、分装、装配等等,形态变化非常快,如何进行追溯、如何进行管控,这是我们碰到的一些挑战。
关于智能化的要求,因为从去年开始我们在工信部发布了智能制造试点示范的专项行动,对智能工厂的要求有五个指标是硬性的指标,运营成本要降低20%,产品的研发周期缩短20%,生产效率提升了20%,产品不良率降低10%,能源利用率提高10%,从这五个指标来看,跟我们自动化设备相关起码有三个,所以自动化、智能化发展是锂电设备发展的方向。我们怎么样做到这几个指标,需要我们动力电池的客户跟我们一起来做一些协作。但是在整个智能装备上,我们的提升是需要客户不断的需求变化来得到提升的。
如图,这个是动力电池智能工厂简单的示意图,包括我们整个智能工厂要做到的一些功能,设备管理、SPC,各个工厂包括分工厂之间的变化,各个工厂的互联。这是自动化形成的情况,就是整个自动化行业的。
自动化的标准是什么?我们现在衡量一个自动化的标准,其实现在只有一个指标,就是你的DPPM或者UPPM,就是每人每天的产量产出,这就是反映工厂自动化程度的标准,所以你的人力在上面用的越少,你的自动化程度越高,这个是我们中间的一个标准。打造这个工厂我们实现自动化、智能工厂信息化,信息化我们就引入了MES系统。然后是智能化,有五个智能化,这是我们对这个行业的要求。关于ERP跟MES的关系,其实在我们锂电行业也碰到这个问题,打个简单的比方,ERP就相当于我们整个公司的销售部门,我们的MES就是我们的生产部门,他怎么执行销售的情况。如图,这个也是ERP跟MES在整个行业里面应用的示意图。
我们赢合助力锂电的智能产线也做了一些调整,第一,我们提供整线的智能生产线的解决方案,我们交钥匙的工程。第二,我们有完整的追溯体系。第三,我们引入的机器人包括立体仓储等等这些措施。包括我们整个追溯系统,引入CCDE等等,包括自动化的提升。
这是我们为了应对整个行业进行了行业资源的整合,包括各个子公司,包括现在的并购,包括行业内的并购,包括在日本设立研究院,为了行业推动做的一些自己的贡献。
我们在创新方面,我刚才也讲了,我们所有的电池设备厂商是配合我们的动力电池厂商做一些工艺的改进,所有的工艺改进必须通过设备或者是一些验证来实现,这块我们是一直全力以赴的在推进。第二,在发展过程中引入立体仓储,这在好几家里面是得到有效验证的,包括自动化上面。还有,我们设备生产的品质管理。还有,我们在整个服务外包,包括我们的设备升级、验证,我们都在做,整个设备多少年以后的服务外包我们全部把它交接过来,包括客户的生产。这是我们整个售后服务,也在这里不再多讲了。
今天我的报告就到这里,希望大家有机会到我们的生产基地,包括在惠州各个分公司里面去考察,因为赢合是一个年轻的公司,也是一个非常Open的公司,我们希望为整个锂电行业的发展做一些自己的贡献。谢谢大家!

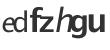
- 最新评论
- 我的评论