由工信部发布的《新能源汽车动力蓄电池回收利用溯源管理暂行规定》于8月1日正式实施,对新能源汽车电池使用过程进行规范化管理。一直以来“赔本赚吆喝”的电池回收行业,也正在迎来一次变革和机遇,有机会告别小规模、低收益的时代。
电动汽车刚刚起步时的“鱼龙混杂”暗藏了很多问题,当初大家忙着造车忙着挣“补贴”,没有人在意电池在未来要怎样处理。而如今随着第一波动力电池退役高峰的到来,造车时忽视的问题正在对电池回收行业产生着巨大影响。
新能源汽车动力电池退役后主要有两个处理方式:梯次利用和回收拆解。但两种方式都面临着共同的问题。
首先,国内电池制造行业缺少统一规范,使得各个品牌的电池在结构、尺寸等方面完全不同,在电池退役后拆解和梯次利用过程中,只能依靠人工拆解,无法形成规模化自动流水作业。但人工作业的可靠性、效率和安全都无法得到保障。
其次,退役电池在梯次利用前需经过品质检测,评估其性能和安全性,完成分级后再进行重组。而在溯源管理规定尚未实施前,退役电池都缺少完整的服役记录,数据的缺失使得对电池品质的评估缺乏准确性,也需要更高的检测成本。重组准确性的降低,也会使得梯次利用后的电池安全隐患增加。
此外,车用动力电池系统是由无数电池电芯通过串联或并联组成模组,再加上电池管理系统和热管理系统组成一个完整的电池包。
对于批次利用,最理想的状态是将电池包拆解为模组后重新组合。如果要将不同批次、不同厂家的电池模组重新组合成新的电池系统,需要对材料、容量、内阻、循环次数等参数做出全面科学的分析,做出合理的分组标准。而我国在这方面的技术实力仍然不够成熟。
前面几个原因不仅增加了电池回收利用的难度,也使得成本增加。而电池回收的主要价值在于正极材料,提取其中的钴、铜、镍、锰等高价值金属。但当金属价格低位徘徊时,回收利用的“经济账”就变得非常不划算。
电池回收需要进行预处理,对电池放电、拆解、粉碎、分选,将有回收价值的材料提取。但电池壳体在生产时大多使用了焊接等刚性连接方式,拆解难度大,而不同正极材料电池的处理流程不同,对废液的无害化处置成本高。经过这样复杂的流程后,回收企业几乎已经无利可图。
“作坊”式生产使得电池回收行业缺乏统一标准和规模化运营,成本高企但收益颇微。不过,随着《溯源管理规定》的发布,以及更多上游车企的加入,整个行业正在逐渐步入正轨。
《溯源管理规定》对电池生产企业、汽车厂家、回收企业、梯次利用企业和再生利用企业的责任和义务做出管理,对每一块电池从出生到退役的数据进行监控,从制度层面逐步规范,有据可循,降低后期再利用难度,也可以避免电池在缺乏监管的情况下被随意处理,污染环境。
而相比国外,我们在电池梯次利用和再生利用方面的技术实力还需要提升,建立回收利用标准。对电池的尺寸、结构如果有标准化的规范,就可以为后期拆解再利用节约大量资源和成本,也为自动化作业创造可能。
资本终究是逐利的,除去技术层面的规范和提升外,如何提升回收与梯次利用的经济效益关系到回收企业的动力和热情。提升金属冶炼效益、降低梯次利用产品成本,都有助于提升回收产业的经济效益。
当然我们也看到了一些好的方向,今年1月中国铁塔股份与比亚迪、银隆、沃特玛、国轩高科等16家企业签订新能源汽车动力蓄电池回收利用合作协议,将退役电池梯次利用于通信基站。
通信基站一般需要后备电源,保证在停电期间可以正常运行,而后备电源对电池的容量和循环寿命要求都不高,使旧电池重组难度变小,同时相比新电池也具备价格优势。中国铁塔拥有近200万座通信基站,未来对电池的需求非常可观。
而随着电池溯源管理规定的逐步落实,电池行业或将进入一个相对规范化、有序化的发展阶段。

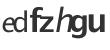
- 最新评论
- 我的评论