电动汽车未来的成功与日益强大的可充电能源的发展有关,特别是锂离子电池组。无论锂离子电池是圆柱形、方形、软包电池还是固态电池,电源的性能将决定电动汽车能否成为汽车市场的主流。
金属连接技术对于锂离子电池的动力发挥至关重要。多年来,超声波金属焊接技术已成为连接这些薄至5 μm、易碎的金属箔片的首选技术。这些箔片是锂离子电池的核心,对于生产可充电电动汽车电源和超级电容器至关重要。
超声波金属焊接也被证明是一种高度通用的技术。除了连接薄而易碎的金属箔片外,它还可以用于组装和连接更厚的电池箔片以及在整个车辆中分配电力所需的大型焊接。这些大型焊接可以包括从厚铜和铝板汇流条到线束和端子的所有焊接应用。这种焊接的多用途性将促使超声波金属焊接技术在电动汽车电池开发和生产方面发挥着重要作用。
超声波金属焊接的工作原理
长期以来,激光或电阻焊接技术被用来熔化材料来粘合高强度含铁金属。然而,当涉及到EV电动汽车电池所需的较软的有色金属箔片时,熔点就成了一个问题。对于有色金属,材料熔化会产生金属间化合物或腐蚀,从而导致材料和连接处过早磨损,引发电池故障。此外,在粘合多个箔层(在某些情况下为100层或更多)时,熔化如此薄且易碎的材料可能会导致几乎无法解决的问题。
超声波焊接不需要熔化材料的表面来连接它们。相反,它对需要被连接的两个金属工件施加高频振动,这两个金属工件被置于“焊头”和“砧座”之间,下工件被砧座上的齿纹 “抓住”并固定到位,机架带动焊头下压上工件,直到上下工件紧密接触并压紧。然后焊头做水平方向的高频振动,产生振动能,清除上下工件接合面的表面污染物和其他涂层。振动产生的摩擦会清除接合面的凹凸不平,产生一个干净、连续的焊接区域,使得原子能跨过接合面,自由扩散到另一方。当振动停止时,这种原子的自由扩散会再结晶成为与冷加工金属相当的细晶粒结构。整个焊接周期在几分之一秒内完成。
振动部件即焊头产生的热量仅相当于每种材料绝对熔点的三分之一至二分之一,从而可以在不熔化材料、不烧穿易碎箔或不产生有害金属间化合物的情况下形成牢固的连接。
图1:超声波金属焊接过程特写,显示焊头、砧座和上下金属工件的位置。向下的压力和水平方向振动(振幅)会产生摩擦,从而在焊接区域实现金属与金属的连接。图片由艾默生必能信提供。
超声波焊接技术多样性的另一个方面是振幅和振动频率可以根据应用的不同而不同。超声波焊接技术足够温和,可以焊接锂离子电池内部的薄而易碎的多层箔片和极耳。锂离子电池使用阳极和阴极集电器。镍和铜极耳和箔通常用于阳极集电器,而铝箔和极耳用于阴极集电器。
对于箔片数量相对较少的电池组件, 通常使用振幅相对较低的40kHz频率来焊接。例如,在方形电池中,40kHz高频低振幅组合简化了焊接过程,并且可以在多层电池设计中连接多达20片铜箔或铝箔。无论电池类型是圆柱形、方形、固态还是新型锂聚合物电池,实践事实证明,超声波焊接是连接这些易碎结构的箔片和极耳的最可靠解决方案。
高品质的超声波金属焊接设备还能够在较大的金属部件与导体、汇流条和线束之间产生牢固的焊接。 当应用需要将多个电池并入电池模块中,然后将模块连接在一起形成电池组时,超声波焊接可以处理汇流条、线束和电缆之间的互连。但对于这些应用,通常使用相对较低的20kHz频率和较高的振幅。在20KHz频率下,超声波金属焊接设备通过消耗高达5500W的功率来进行高达80微米的水平运动。这种低频/高振幅应用通常用于电动汽车的大型电池组,以及专用采矿车、大型无人机和其他特殊车辆,其中的方形电池根据焊接尺寸和面积,可以将100多层的箔片焊接到单个极耳上。
超声波金属焊接工艺的优势
· 适用于各种有色金属材料
· 在不同金属之间建立永久的冶金结合
· 无需熔化 — 材料的化学或冶金性能无变化
· 非常适合焊接高导电合金;材料的反应性无关紧要
· 不产生金属间化合物、微粒或引起腐蚀的反应
· 非常适合连接薄且易碎的金属薄膜和结构
· 多种控制方法可实现流程定制、高重复性和统计过程控制SPC (Statistical Process Control)
· 低能量输入(能耗比熔焊或电阻焊低 30 倍);无耗材
· 总成本低于其他各类焊接工艺
精确控制确保焊接质量的一致性
超声波金属焊接基于三个基本控制因素来确保焊接质量:能量控制、振幅控制和焊头夹具质量。
· 焊接能量控制
超声波焊接提供三种不同的焊接模式来提供能量控制:时间、高度和能量。时间模式要求每次焊接的周期时间保持一致。高度模式要求焊接到预设的焊接高度。能量模式对每个焊接周期应用相同的能量。
能量模式是首选模式,因为它允许焊机自动补偿被接合材料表面状况的任何差异。例如,一些需要接合表面可能有不同程度的污染,当振动开始时,这将需要更多的“摩擦”,以建立完全的金属对金属的表面连接合。能量模式能够补偿这些差异,而高度和时间模式则不能。
能量模式计算公式如下:
· 焊接振幅控制
在下压力的作用下,焊头压紧被焊工件到砧座上,焊头带动上工件在焊接区域的振动距离被称做焊接振幅。对振动幅度的要求通常是根据被焊接材料的类型和状况确定的,并且通过焊接设备的发生器、换能器和上焊头协同工作对每个焊接周期实施精确控制。
· 焊头夹具
焊头夹具是指砧座和焊头, 其设计和材料组成。超声波焊头能够抓住上部金属工件至关重要,这样它才能提供准确的振动横向力,从而实现与下部金属工件的结合。这种抓握是通过对焊头的表面进行特殊加工来实现的,就是把焊头的表面制作成球形、菱形或锯齿状歯纹,在振动过程中能够牢牢夹持住上工件,下部金属工件由下部砧座固定到位。超声波焊机精确管理这些重要控制因素, 确保通过超声波焊接技术获得一致的焊接质量。
焊接过程记录
对于许多制造商而言,通过技术手段记录产品质量变得尤为重要。各行各业都要求记录产品装配和制造数据,并根据需要提供这些数据,以符合监管准则、支持客户服务或满足产品保修要求。
幸运的是,高质量的超声波焊接设备内置实时监控和处理焊接数据的能力,使制造商能够更有效地满足多样化和日益严苛的质量保证要求。
未来的挑战和承诺
电动汽车制造商开发和制造先进、高功率电池的能力与金属焊接过程的各个方面密切相关——焊接设备质量、焊接模式控制、焊头夹具的精度和耐用性、数据收集和通信能力以及及时的乃至全球范围内的技术支持。幸运的是,超声波金属焊接技术已被证明是首屈一指的金属连接工艺,它可以满足工业规模所要求的高重复性,高可靠性和高生产效率的质量要求。
作者简介
杨约邦,艾默生必能信全球金属焊业务发展经理。在行业里深耕二十年,带领着必能信超声波金属焊接的销售,应用和业务发展。本科毕业于香港理工大学机械工程系。
补充图片:
图片说明:艾默生Branson? GMX-20MA超声波金属焊接设备在精度和功率方面的持续改进使新一代电动汽车电池的开发和组装成为可能。照片由艾默生必能信提供。
图片说明:艾默生的 Branson? GMX-20DP超声波金属直压焊接设备利用高压力、低振幅的设计,针对电池簿材焊接能减少损坏和粉尘。照片由艾默生必能信提供。
图片说明:超声波金属焊接可以焊接相对较粗的电缆、汇流条和端子。由于该过程在不熔化导电金属的情况下连接它们,因此金属材料本身的完整性和特性不受影响。照片由艾默生必能信提供。
图片说明:超声波焊接提供了成熟、可靠的解决方案,用于接合通常用作阳极集电器的铜箔和极耳。照片由艾默生必能信提供。

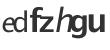
- 最新评论
- 我的评论